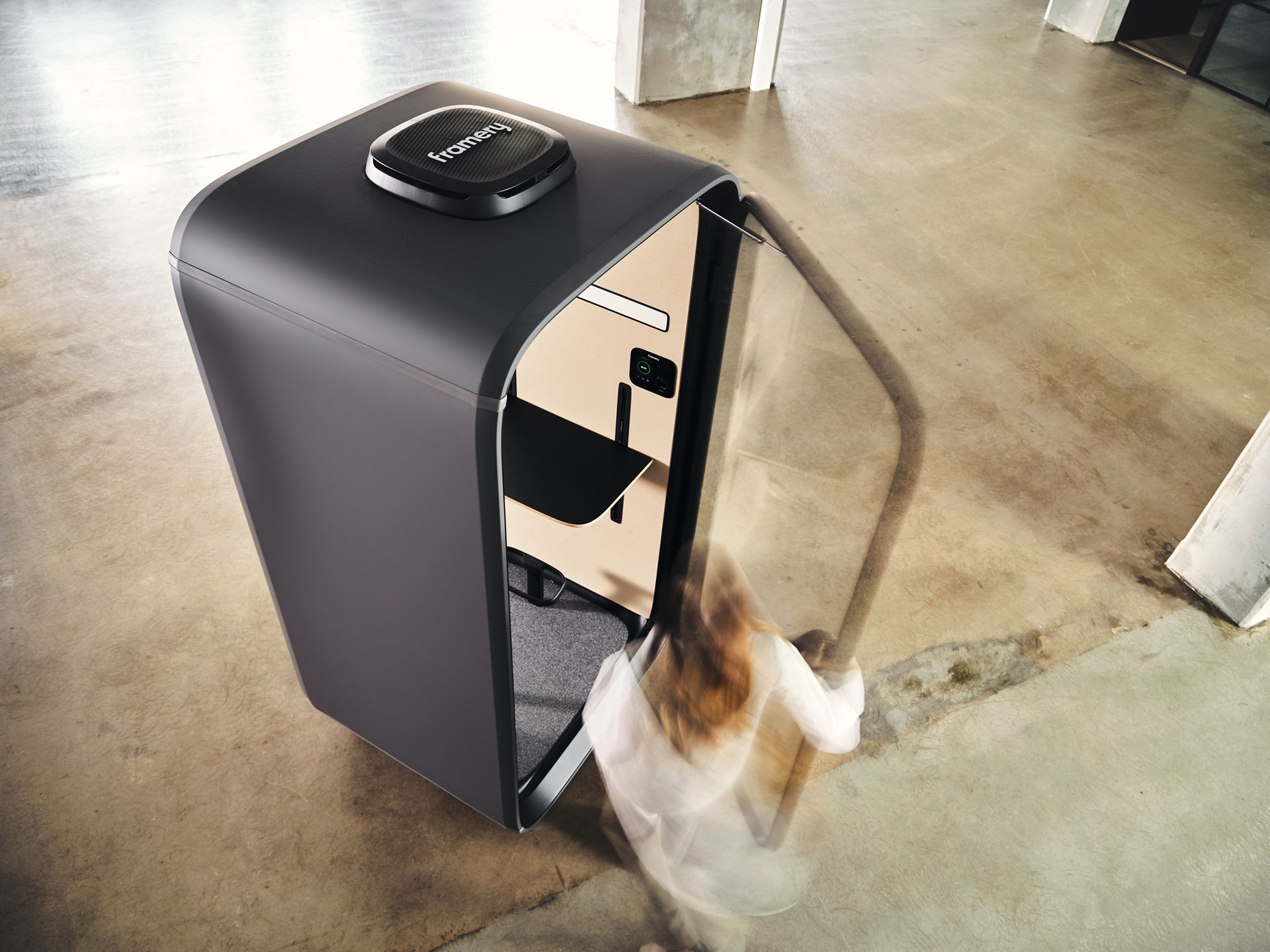
Founded in 2010, Framery is a pioneering company in manufacturing and developing soundproof telephone booths and workspaces. The products solve noise and privacy problems in the offices of dozens of the world’s leading companies. Up to 70% of the Forbes top 100 companies use Framery.
MSK Plast manufactures a range of injection moulded plastic parts for Framery’s telephone booths. The smooth and professional cooperation has brought more efficiency and flexibility to Framery’s production.
The cooperation between Framery and MSK Plast started in 2019 with the Framery One model. The company’s product range has grown year after year, and today the company designs and manufactures various products in different sizes and suitable for different types of work. Today, MSK’s plastic parts are used in several of the company’s phone booth models.
“As a partner with MSK, we appreciated right from the start that they are local, reliable and always have a good service level. We immediately had a relaxed, uncomplicated communication and conversation. If we encountered challenges, we could communicate and work through them effortlessly,” praises Framery’s Product Manager, Henrik Ashorn.
They are local, reliable and always have a good service level
Injection moulded plastic parts for many different applications
MSK Plast manufactures parts for Framery booths, including parts for cladding activated carbon filters and ventilation ducts. In addition, in Framery’s older products, the guide pins between the wall, ceiling and floor modules are supplied by MSK.
One of the most prominent plastic parts is found in the seams of the Framery One’s exterior, finished with narrow trim strips about a meter long, made by MSK. The finishing of the parts requires precision, as the trim strips remain neat and tidy, with no suction marks from, for example, moulding. In addition, the list is slightly translucent, with a dedicated light behind the booth that shines through.
“Framery One is available in eight different colours, so the trim lists are also made in the same colour and are matched to the matte finish panel. The Corona era presented us with new challenges, as the special colors that MSK ordered for us and used in the parts came from Italy, while the manufacturing of prototypes was done in China. We could not see the initial parts on site, so we had to inspect them only from the pictures sent from China and checked the final situation in Finland. However, the cooperation with MSK was flexible, and we could get things rolling quickly even in this situation,” says Ashorn.
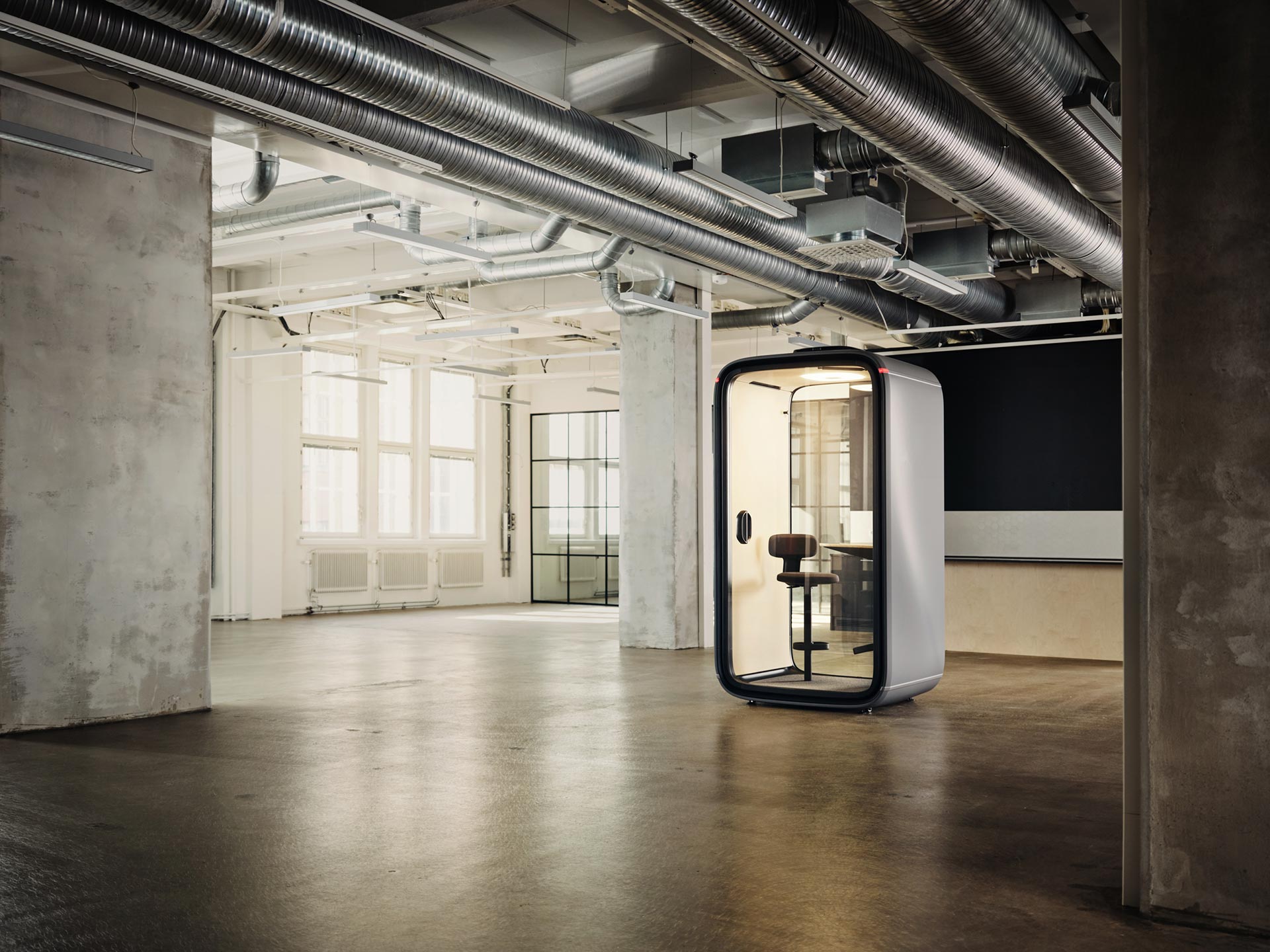
Flexible cooperation is the key
The cooperation between MSK and Framery also extends to the design of parts and works partly hand in hand. MSK’s role is to ensure that the part makes sense to deliver the most functional, manufacturable product possible. For Framery, the collaboration has also meant, above all, a cost-effective way to manufacture parts. The parts from MSK also give Framery flexibility in its operations.
“From MSK Plast, we get the finished part and don’t have to do any further processing. The finished part goes straight to the customer’s packaging, which only goes through us because the booth is packaged here. At Framery, we rely on the quality and professionalism of MSK,” sums up Ashorn.